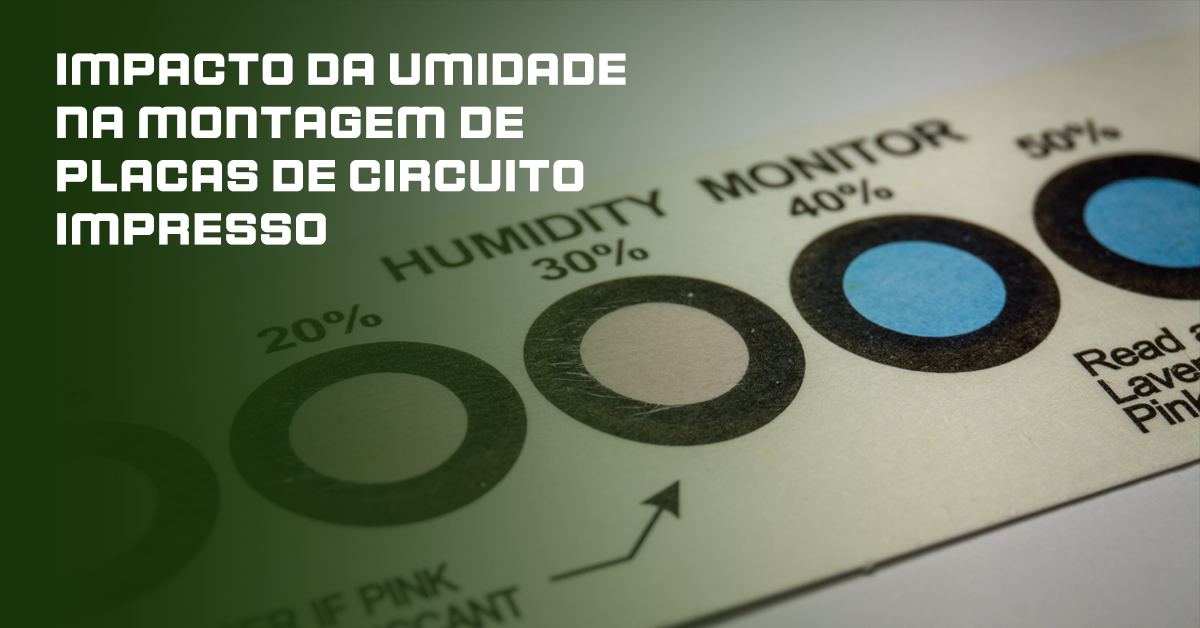
Em nosso último post falamos sobre as principais formas de proteção das placas de circuito impresso capazes de blindá-las após a fabricação da placa nua e da montagem dos componentes. Porém, os cuidados durante esses processos também são fundamentais para a longevidade e segurança dos produtos, já que esses revestimentos de proteção irão impedir a entrada de umidade. Contudo não atuarão completamente sobre a umidade já existente na placa oriunda dos processos de fabricação anteriores.
A umidade absorvida durante o processo de produção e montagem de placas de circuito impresso pode causar uma série de problemas. São eles: a corrosão de componentes, falhas na integridade do circuito, atraso na transmissão dos sinais, bem como aumento dos atrasos de propagação e consequente, mau funcionamento dos dispositivos eletrônicos.
E dentre os principais problemas detectados, temos a delaminação de camadas da placa, falhas no processo de soldagem e a oxidação chegando inclusive à corrosão de componentes metálicos.
O que torna a situação mais crítica é que eventuais problemas podem ocorrer somente após algum tempo depois da utilização do produto já em campo, o que multiplica os custos de reparação.
Ao lidar com umidade em placas de circuito impresso, é importante compreender os conceitos básicos, como umidade relativa, ponto de condensação e absorção de umidade. A umidade relativa influencia a velocidade de absorção de umidade pelas placas, enquanto o ponto de condensação indica as condições em que a umidade se transforma em água. Compreender esses conceitos é fundamental para o desenvolvimento de estratégias eficazes de mitigação e controle da umidade.
Dentre as principais fontes de umidade podemos citar a do ar, água residual de processos de limpeza, vazamentos e condensação, sendo fundamental identificar e controlar essas fontes para garantir a integridade das placas de circuito impresso.
Uma ameaça ainda pior é a condensação, que ocorre quando a superfície da PCB está mais fria do que o ambiente. A condensação pode formar-se tanto nas faces externas da placa como no interior dos pacotes de componentes que devem, portanto, ser selecionados levando em consideração este aspecto.
Diversas tecnologias estão disponíveis para mitigar os efeitos da umidade na produção e montagem de placas de circuito impresso. Entre elas, destacam-se o uso de sistemas de desumidificação, que controlam ativamente os níveis de umidade nas instalações, a utilização de materiais laminados e revestimentos resistentes à umidade, e a implementação de câmaras de vácuo para processos críticos. Além disso, a utilização de tecnologias de soldagem a vácuo e o emprego de técnicas de encapsulamento hermético são eficazes para proteger as placas contra a umidade durante a montagem.
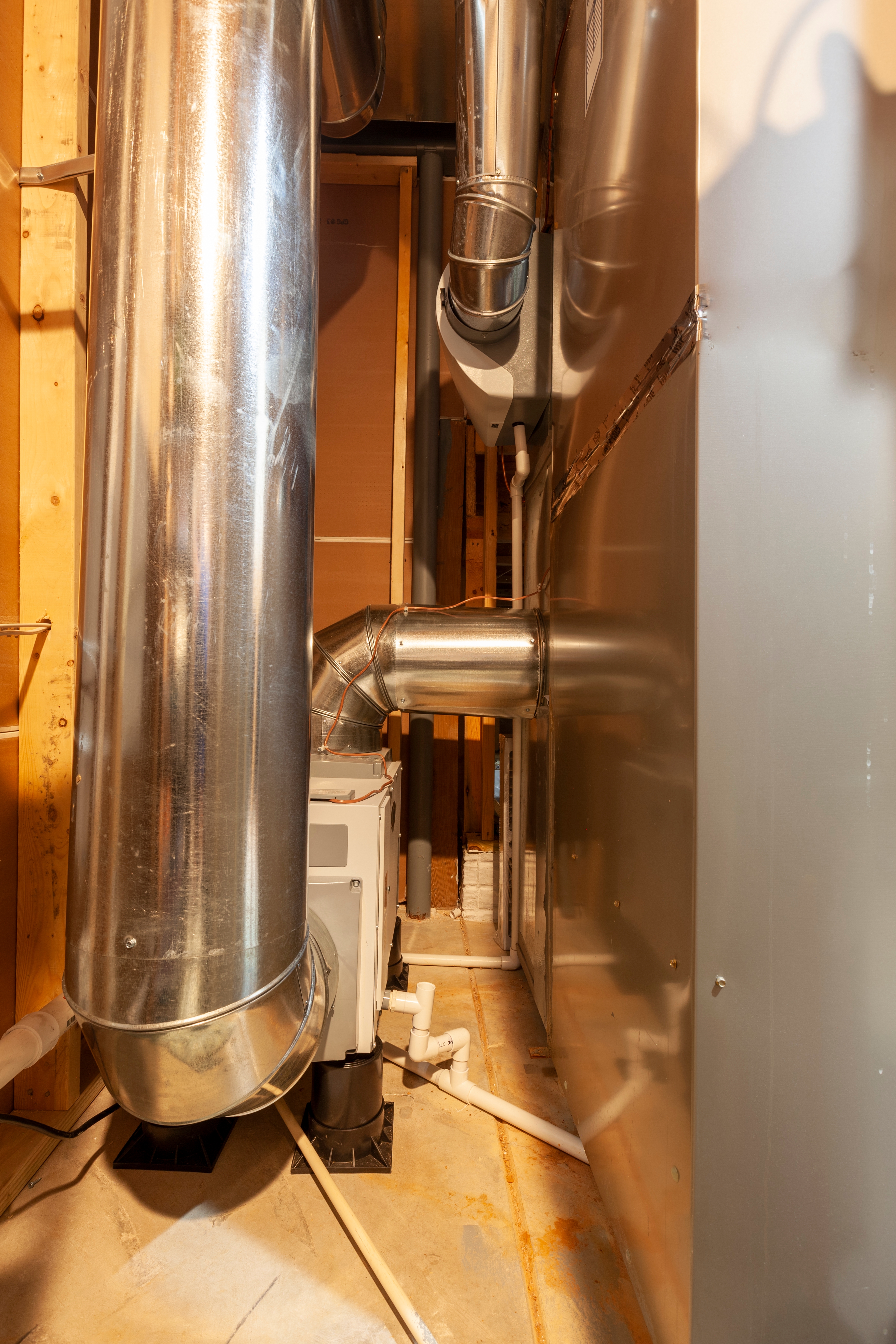
Durante a fabricação das placas de circuito impresso de multicamadas, os cuidados devem ser redobrados pois no processo de laminação a temperatura e umidade precisam ser rigorosamente controladas. O manuseio deve incluir o uso de luvas, evitando assim a contaminação entre os diferentes componentes. Durante o processo de laminação é importante se aplicar um efeito de vácuo de baixa pressão, para que não se formem fendas capazes de reter a umidade.
Para minimizar os efeitos da umidade relativa do ar, que pode variar substancialmente dependendo das condições climáticas, deve-se adotar práticas de controle de umidade na fábrica. Isso inclui o uso de dessecantes como sílica-gel, zeólitos e argilas ativadas, que atuam como barreiras para impedir a penetração de umidade nas placas. Além disso, é importante manter um ambiente controlado e com baixa umidade relativa, bem como utilizar embalagens herméticas para armazenar as placas antes da montagem. Os sachês dessecantes desempenham um papel fundamental. Eles são substâncias que absorvem a umidade do ar, evitando a condensação sobre as placas de circuito impresso. É importante escolher o dessecante adequado, levando em consideração o ambiente de produção e as condições de armazenamento das placas.
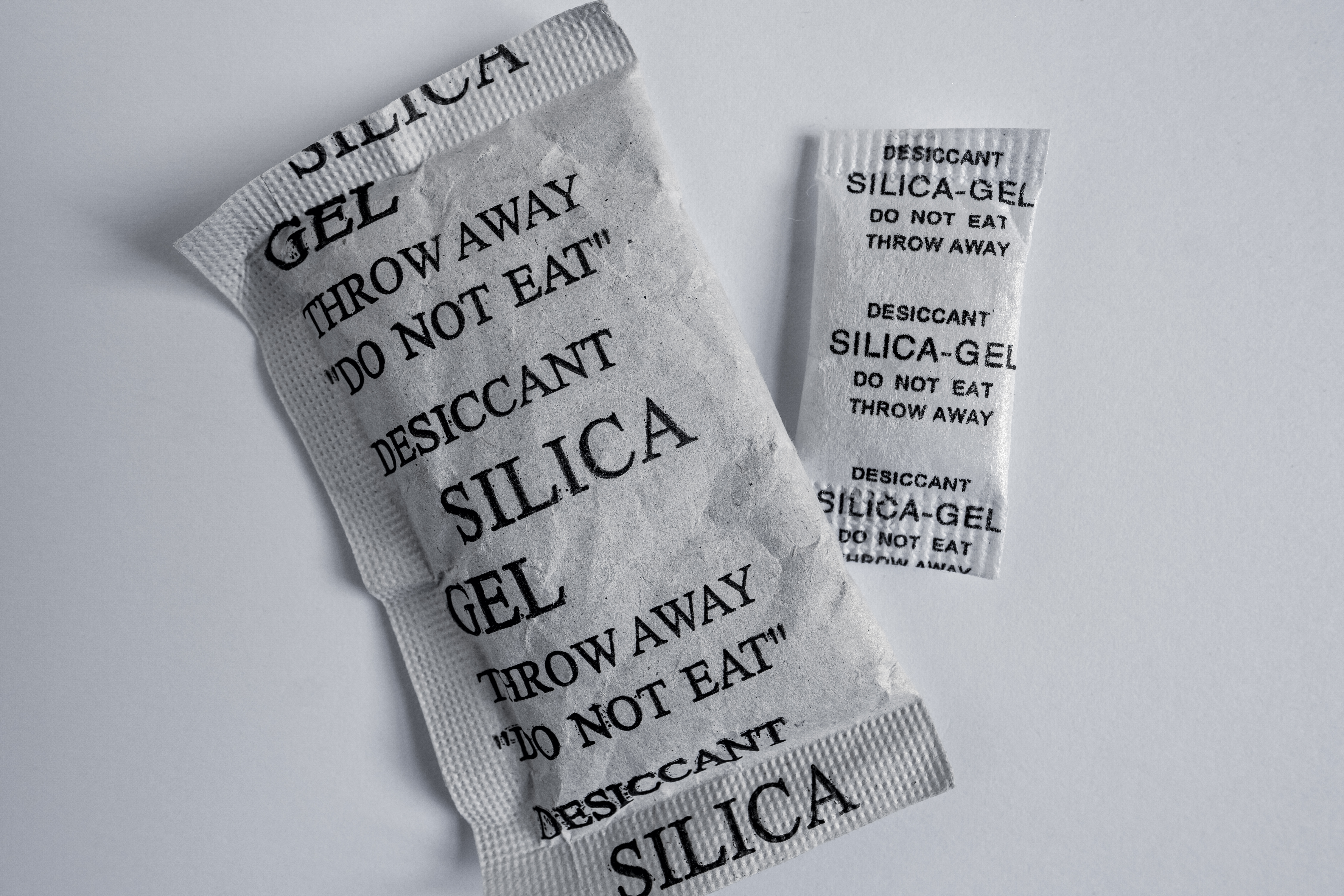
O armazenamento correto dos componentes eletrônicos é crucial para evitar a umidade durante a montagem de placas de circuito impresso. Componentes sensíveis à umidade devem ser armazenados em embalagens herméticas com indicadores de umidade para garantir que não sejam expostos a níveis excessivos de umidade. Também é importante manter os componentes eletrônicos em ambientes com controle de temperatura e umidade, de preferência em salas com condições controladas.
Inovações na área de secagem a vácuo, atmosferas controladas e utilização de tecnologias de ponta, como micro-ondas e luz infravermelha, melhoraram muito o processo de eliminação de umidade em placas de circuito impresso.
Os padrões de controle de umidade em placas de circuito impresso lançados pelo IPC em 2010 indicam também a cozedura como um método prático para removê-la dos PCBs, caso não tenha sido possível impedir a sua entrada anteriormente.
Depois de concluída a montagem dos componentes na placa, cozinhar no forno é uma prática comum e eficaz para remover a umidade. Porém, é necessário garantir que o coeficiente de expansão térmica (CTE) do material utilizado para a PCB não seja ultrapassado, evitando assim delaminação ou trincas.
Existem várias técnicas de cozimento de placas de circuito impresso para eliminar a umidade, incluindo o uso de estufas de secagem, fornos de vácuo e fornos de convecção. O método mais comum é o uso de estufas de secagem, que funcionam expondo as placas de circuito impresso a altas temperaturas por um certo período de tempo. Já os fornos de vácuo são eficazes para assegurar que a umidade seja removida de maneira mais rápida e completa. Por fim, os fornos de convecção utilizam ar forçado para acelerar o processo de remoção de umidade, sendo uma opção eficiente para placas de circuito impresso com componentes sensíveis ao calor.
Durante o processo de cozimento das placas de circuito impresso para eliminar a umidade, é essencial considerar a temperatura como um dos principais parâmetros. Ela deve ser controlada com precisão, pois se muito baixa pode não eliminar totalmente a umidade, enquanto uma temperatura muito alta pode danificar os componentes. O período de cozimento deve ser suficiente para eliminar a umidade, sem prolongar excessivamente para evitar danos. A uniformidade da distribuição de calor também é importante, garantindo que todas as áreas da placa sejam aquecidas de maneira adequada e que a umidade seja eliminada de forma homogênea.
No entanto, a cozedura no forno traz outros inconvenientes como aumento de custos, dos tempos de produção e uma menor soldabilidade. Portanto, é um método a ser evitado sempre que possível, através do controle rigoroso dos processos.
É claro que todos esses cuidados se tornam mais ou menos necessários de acordo com a sensibilidade à umidade dos componentes presentes na placa. Componentes eletrônicos identificados pela sigla MSD (Moisture Sensitive Device) é que precisam de cuidados redobrados, isso desde seu armazenamento antes mesmo de entrar no processo de montagem e até mesmo o armazenamento da placa já montada.
As técnicas de teste e análise de umidade são essenciais para garantir a qualidade das placas de circuito impresso. Através de métodos de medição precisos, é possível identificar os níveis de umidade presentes no ambiente de produção e durante a montagem das placas. Além disso, essas técnicas permitem analisar os efeitos da umidade na integridade e desempenho das placas, possibilitando a implementação de medidas corretivas e preventivas para minimizar os impactos negativos.
Os métodos de medição de umidade utilizados incluem técnicas como termogravimetria, análise térmica dinâmico-mecânica, espectroscopia no infravermelho, entre outros. Essas técnicas possibilitam a medição precisa da umidade presente em materiais como resinas, substratos e componentes eletrônicos.
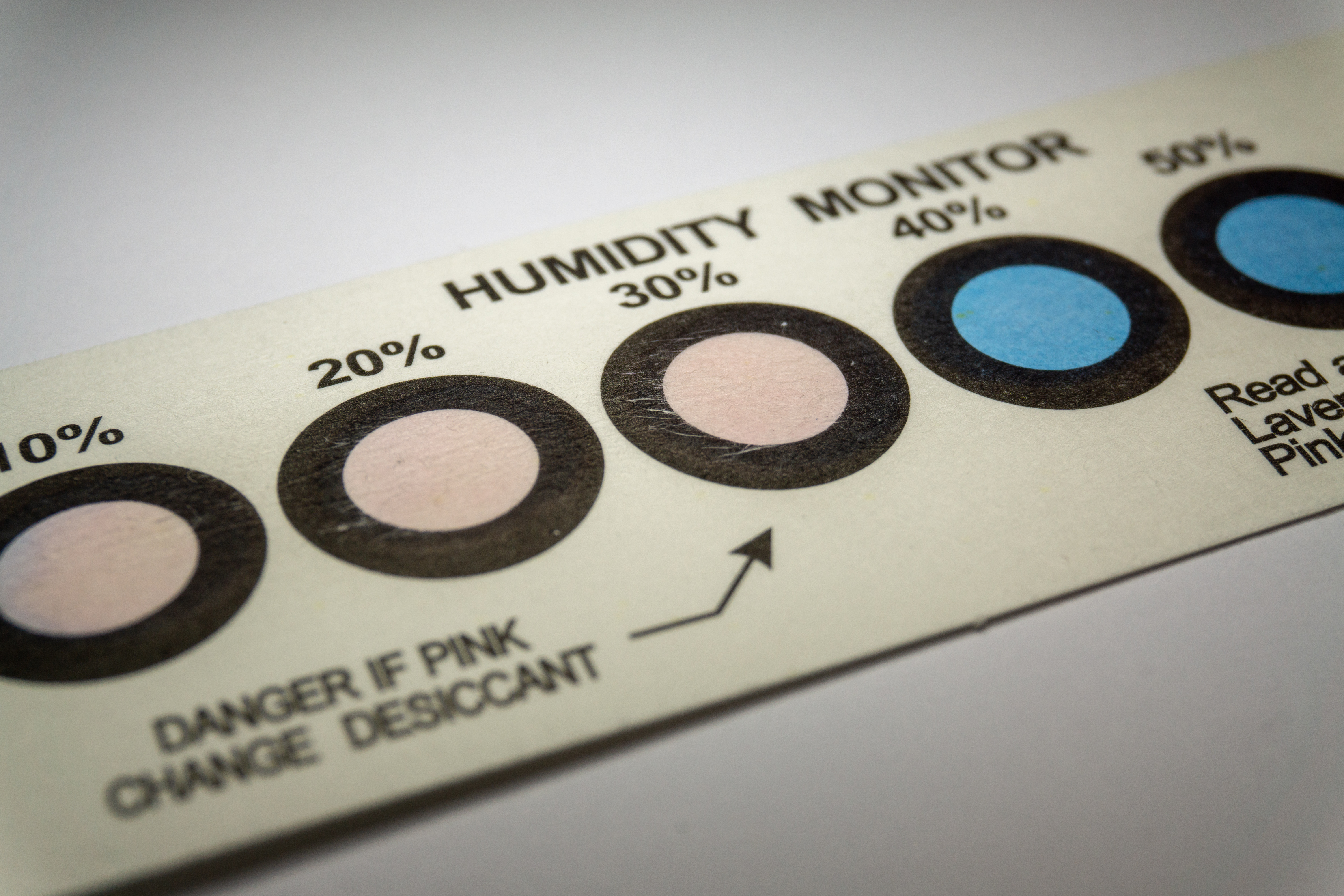
Os padrões IPC para orientar os fabricantes de eletrônicos (IPC/JEDEC JSTD-020E e IPC/JEDEC J-STD-033D), dividem níveis de sensibilidade à umidade, em classes de 1 a 6 de acordo com a suscetibilidade aos riscos causados por ela. Cada nível estipula um tempo máximo em que o componente possa ficar exposto a ambientes sem proteção contra a umidade sem que seja necessário submetê-lo ao processo de cozimento em fornos para retirar a umidade absorvida.
Interessante notar que no nível 6 os componentes mais sensíveis precisam passar pelo cozimento mesmo antes de terem sido utilizados. Veja a tabela:
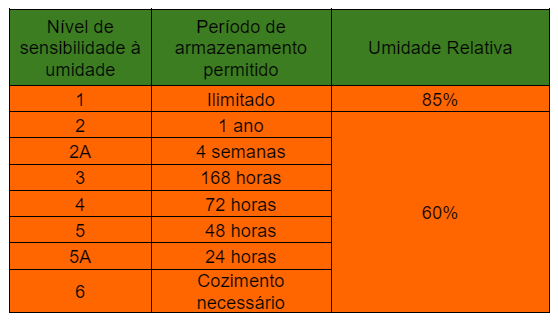
As normas e recomendações industriais relacionadas à umidade na produção e montagem de placas de circuito impresso incluem diretrizes para o controle ambiental, armazenamento e manuseio de materiais sensíveis à umidade, bem como o uso adequado de dessecantes e selantes. As normas também estabelecem procedimentos de teste e análise de umidade, garantindo que os produtos atendam aos padrões de qualidade e confiabilidade.
Os padrões de umidade aceitáveis para placas de circuito impresso variam de acordo com o tipo de material e os requisitos específicos de cada aplicação. Normalmente, os padrões estabelecem níveis máximos de umidade permitida durante a produção, armazenamento e montagem.
Aqui na TEC-CI adotamos todos os padrões e normas visando a máxima redução possível dos níveis de umidade em nossas placas, garantindo aos nossos clientes processos de montagem mais estáveis e os melhores resultados finais em seus produtos.