Como reduzir os custos das placas de circuito impresso através do layout
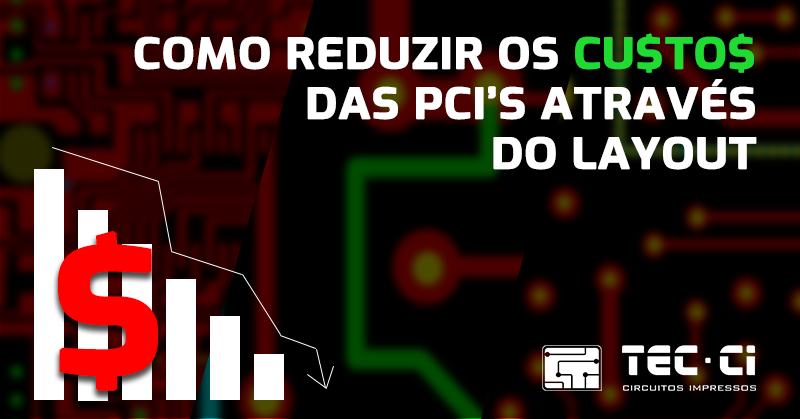
Em mais de 30 anos no mercado de placas de circuito impresso, já vivenciamos inúmeras situações onde pudemos orientar nossos clientes a efetuar mudanças simples no layout que, não somente agilizaram o processo de fabricação e montagem, como também reduziram o custo final das placas. Além disso, para auxiliar nossos clientes, também desenvolvemos um ranking dos melhores e mais utilizados softwares EDA para geração de layout de placas de circuito impresso.
Veja a seguir os erros mais comuns que levam ao aumento dos custos e saiba como evitá-los, reduzindo de forma significativa o preço final da sua placa de circuito impresso.
1 – Pontos críticos desnecessários
A determinação do processo de transferência de imagem a ser utilizado na fabricação de uma placa de circuito impresso, e a velocidade em que esse processo será executado, depende da complexidade gerada no layout. Placas com espaçamentos entre trilhas ou ilhas muito pequenos, ou trilhas finas demais, por exemplo, podem obrigar a utilização de processos de transferência de imagem fotográficos, que por mais que estejam tão bem difundidos entre os fabricantes de placas de circuito impresso, sempre serão mais caros que os processos tradicionais, como impressões serigráficas. Então sempre que possível, o layoutista deve evitar essas situações equilibrando da melhor maneira possível a largura das trilhas e o diâmetro das ilhas com o espaçamento entre todos os pontos.
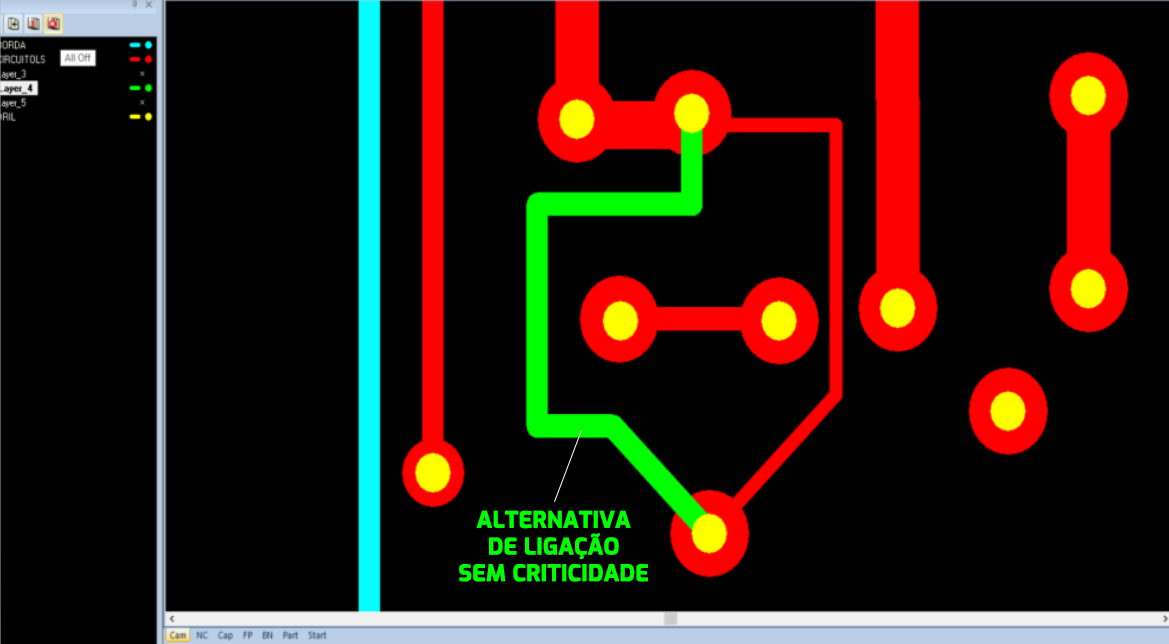
Pontos críticos desnecessários
2 – Muitas variações de diâmetro
A crescente velocidade das máquinas de furação por comando numérico (CNC), vem no decorrer dos anos reduzindo o custo deste importante processo que é a furação. Conforme o diâmetro a ser furado, faz-se diversos movimentos de penetração em um único segundo. Numa máquina com 6 spindles de furação por exemplo, e abaixo desses spindles “sanduiches” de até 4 placas, pode-se fazer centenas de furos em apenas 1 segundo.
A cada troca de broca para se executar um novo diâmetro, entre a desaceleração, deslocamento e aceleração do spindle, são gastos cerca de 20 segundos. Ou seja, a cada troca de broca, se deixa de fazer algo em torno de 2000 a 2500 furos com o mesmo custo. Muitas vezes recebemos arquivos de furação com lista de diâmetros com diferenças centesimais entre um diâmetro e outro, por exemplo, furos de 1,10mm / 1,15mm / 1,20mm / 1,25mm / 1,30mm, além de vários outros diâmetros na mesma placa. Quase sempre que resolvemos checar com o nosso cliente se ele realmente precisa dessas variações, ele se dá conta de que esses diâmetros foram definidos individualmente para cada componente e não precisam ter toda essa variação. Assim, unificações de diâmetros simples, como alterar os furos de 1,15mm para 1,20mm e os de 1,25mm para 1,30mm, por exemplo, irão reduzir o número de trocas de brocas, acelerando consideravelmente o processo de furação sem causar nenhum prejuízo ao projeto da placa, gerando economia de tempo que certamente refletirá em melhores preços e prazos de entrega.
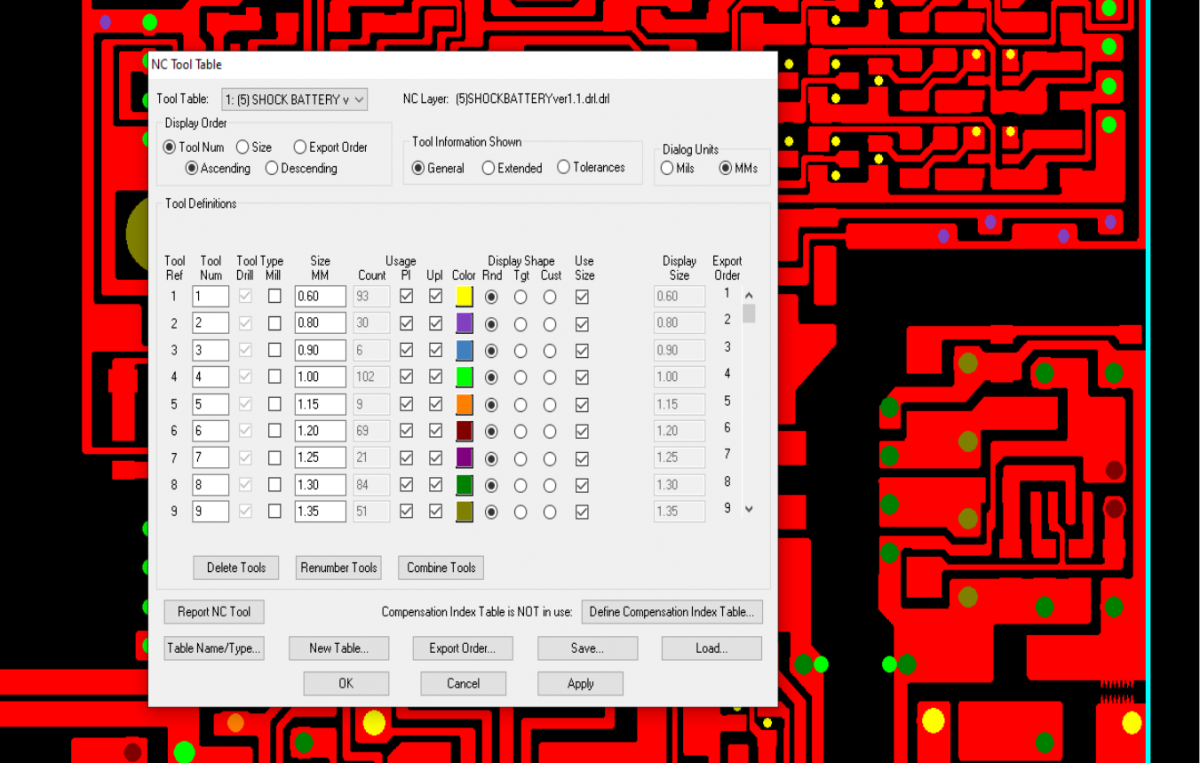
Muitas variações de diâmetro
3 – Furo ou rasgo
Existem muitos componentes que possuem seu terminal retangular ou quadrado, e as vezes por distração, alguns layoutistas acabam determinando que o orifício para a inserção desses componentes seja também um quadrilátero. É claro que muitas vezes por questões mecânicas e também para uma melhor soldabilidade, isso é inevitável. Porém, há muitas situações, principalmente em orifícios pequenos, em que a utilização de furos redondos em nada prejudica a fixação ou a soldabilidade desse componente, e o processo de furação é muito mais rápido e consequentemente mais barato do que o processo de fresagem, utilizado para se fazer orifícios retangulares.
Contudo, vale lembrar de um erro muito comum que verificamos na conversão desses orifícios quadrados em furos redondos: um rasgo quadrado com lados de 2mm, por exemplo, quando transformado em furo deverá ter um diâmetro maior do que 2mm, pois na verdade para que a inserção do componente seja possível em um furo redondo, deve-se considerar a medida da diagonal deste quadrado. Então, como Pitágoras nos ensinou, podemos calcular que a diagonal do nosso exemplo medirá aproximadamente 2,83mm. Nesse caso, um furo de 2,90mm seria o indicado, pois garantiria uma boa inserção e minimizaria riscos de problemas de soldabilidade.
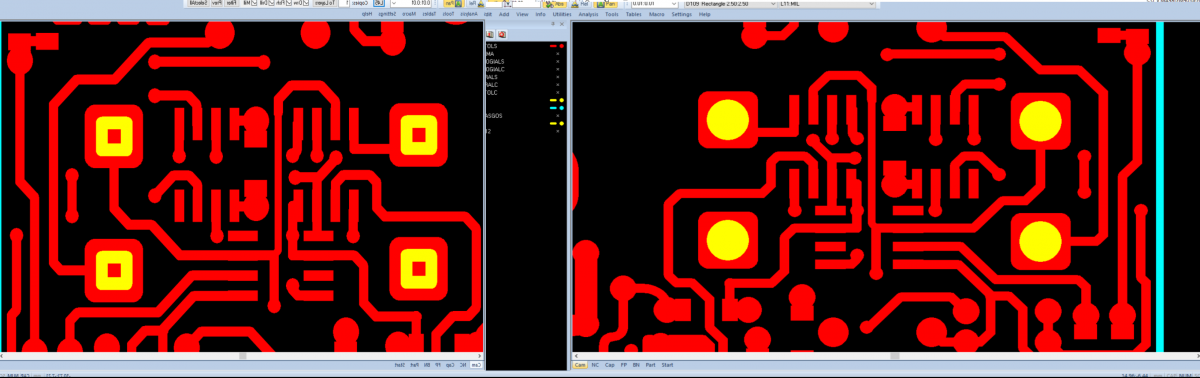
Orifícios quadrados (rasgos) | Substituição por furos redondos
4 – Aproveitamento de áreas livres no painel
Existem situações onde um modelo possui corte irregular, em formato de “L” por exemplo, e dependendo de cada caso, é possível inserir uma outra placa de dimensões menores nesse espaço que seria perdido. Porém, ao fazer a unificação, é sempre importante verificar se o processo de separação dessas placas, tanto antes quanto após a montagem, não irá gerar custos que anulem suas vantagens.
É importante observar também se as placas possuem as mesmas características básicas, como o mesmo laminado, de mesma espessura, com máscara e legenda da mesma cor, densidade de trilhas similares etc, assim pode-se reduzir esses custos unificando mais de um modelo em uma mesma placa.
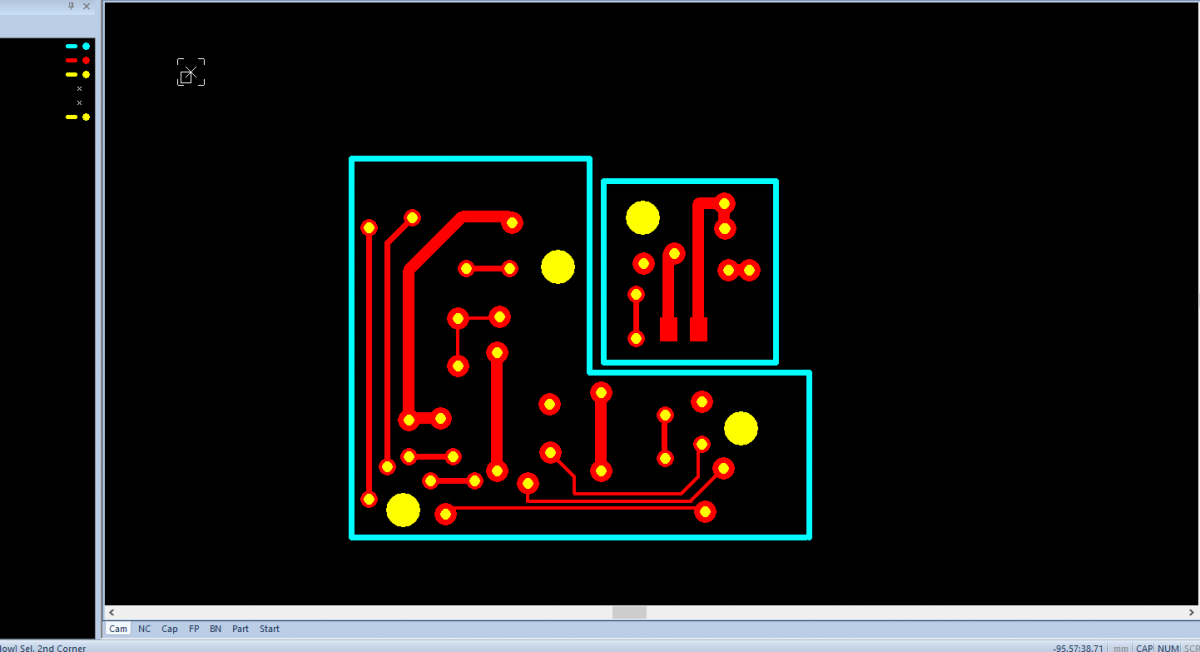
Aproveitamento de áreas livres no painel
5 – Dimensões de painéis incompatíveis com equipamentos e laminados disponíveis no mercado
Ao determinar um painel com várias placas para obter uma melhor produtividade na linha de montagem, é importante sempre que possível que se determine uma multiplicidade, que gere medidas compatíveis com os equipamentos não só da linha de montagem, como também com os equipamentos de fabricação das PCI’s. Além disso, painéis com medidas que gerem um bom aproveitamento das chapas de laminados a serem utilizados.
Imagine uma placa de 50mm x 50mm, onde se resolva fazer um painel de 350mm x 350mm. Isso significa 7 vezes a placa em cada lado desse painel. Esse painel (7×7) terá 49 peças dentro dele.
Agora imagine uma chapa de laminado que mede por exemplo 1020mm x 1220mm. Desta chapa, só será possível se fracionar 6 painéis de 350mm x 350mm, e se cada painel tem 49 peças, então em uma chapa de laminado seriam produzidas apenas 294pçs.
Caso esses painéis tivessem 300mm x 400mm teríamos então 48 peças de 50mm x 50mm dentro dele (6×8), e em cada chapa de laminado de 1020mm x1220mm conseguiríamos extrair 9 painéis, ou seja, teríamos então um total de 432 peças.
É claro que os retalhos que sobrariam no primeiro exemplo ainda poderiam ser utilizados para outros modelos de placas ou até comercializados, porém também é bastante claro que este excelente aproveitamento do laminado do segundo exemplo poderá certamente pesar bastante para se conceder aquele importante desconto na hora de uma possível negociação. Mas, como as medidas acima são apenas exemplificativas e variam de um laminado para outro, é importante consultar no momento de determinar o formato do painel de produção quais seriam as opções que possam gerar um melhor aproveitamento, e é claro, sem prejudicar o processo de montagem que também tem suas limitações dimensionais.
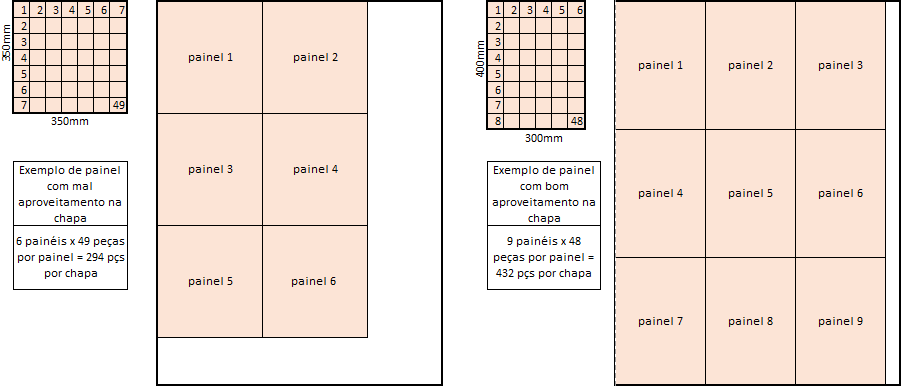
Dimensões de painéis incompatíveis com equipamentos e laminados disponíveis no mercado
6 – Contornos especiais nem sempre inevitáveis
Contornos podem ser executados em guilhotina, podem ser vincados, estampados ou fresados. De todos os processos para se cortar uma placa, a fresagem é de longe a de maior custo. Placas de circuito impresso com reentrâncias e saliências em lotes que não justificam a fabricação de ferramentas para estampagem, acabam tendo que ser fresadas, mas as vezes essas situações podem ser revertidas.
Muitos projetos podem ser repensados, alterando-se formas de fixação da placa, modificando-se caixinhas, racks e gabinetes ou até mesmo alterando apenas detalhes na própria placa. Cortes em “L” para se desviar de algum obstáculo por exemplo, algumas vezes podem ser substituídos por cortes retos na diagonal.
Uma alternativa interessante verificada em algumas placas é a utilização de uma sequência de furos que formam um “picote”, para a formação de um determinado contorno sem a necessidade de fresagem.
Placas redondas muito frequentes desde o surgimento da iluminação por leds, podem muitas vezes ser substituídas por placas quadradas, hexagonais, octogonais etc. É claro que quanto mais faces de corte guilhotinados se criar, os custos também tenderão a crescer, mas dificilmente atingirão os custos de fresagem que quase sempre serão maiores.
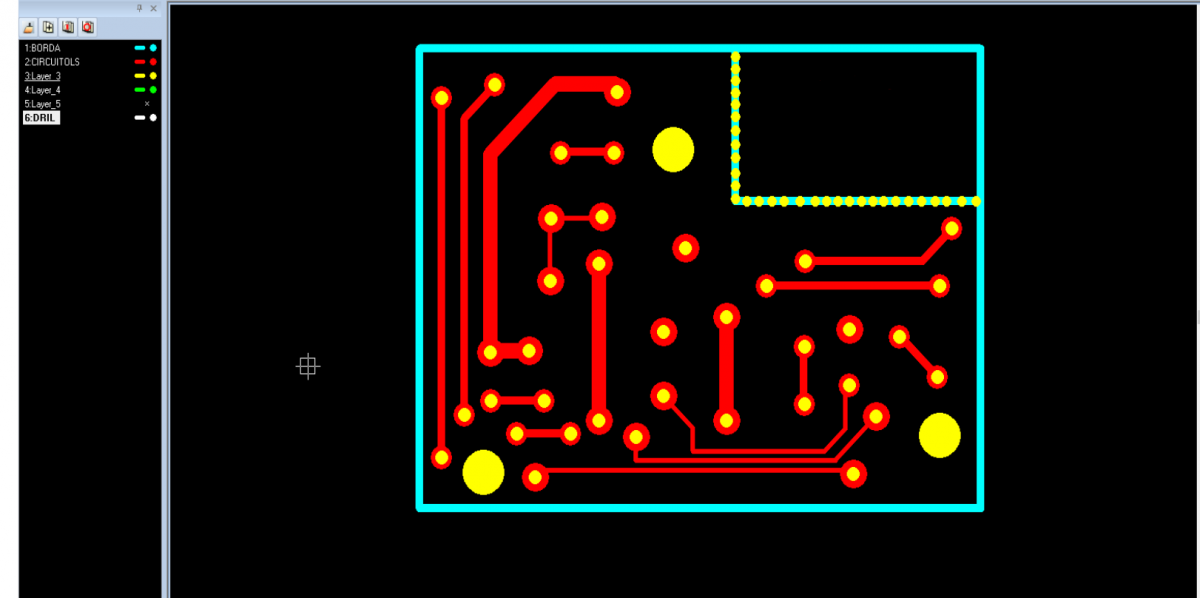
Contornos especiais nem sempre inevitáveis
7 – Tolerâncias intoleráveis
A determinação de tolerâncias nas dimensões mecânicas da placa a níveis extremamente restritos, pode obrigar a se adotar processos de fabricação mais caros e nem sempre essas tolerâncias são realmente necessárias. É muito comum ver uma única medida de tolerância adotada para toda a placa, e muitas vezes essa tolerância adotada é necessária em apenas um ponto específico. Recomendamos então, sempre que possível, que se determine uma tolerância mais ampla para toda a placa e especifique somente nos pontos necessários aquelas que realmente precisam ser menores. Assim, processos mais rápidos e não menos eficazes poderão ser adotados sem que seja incluído um componente de custo desnecessário à placa.
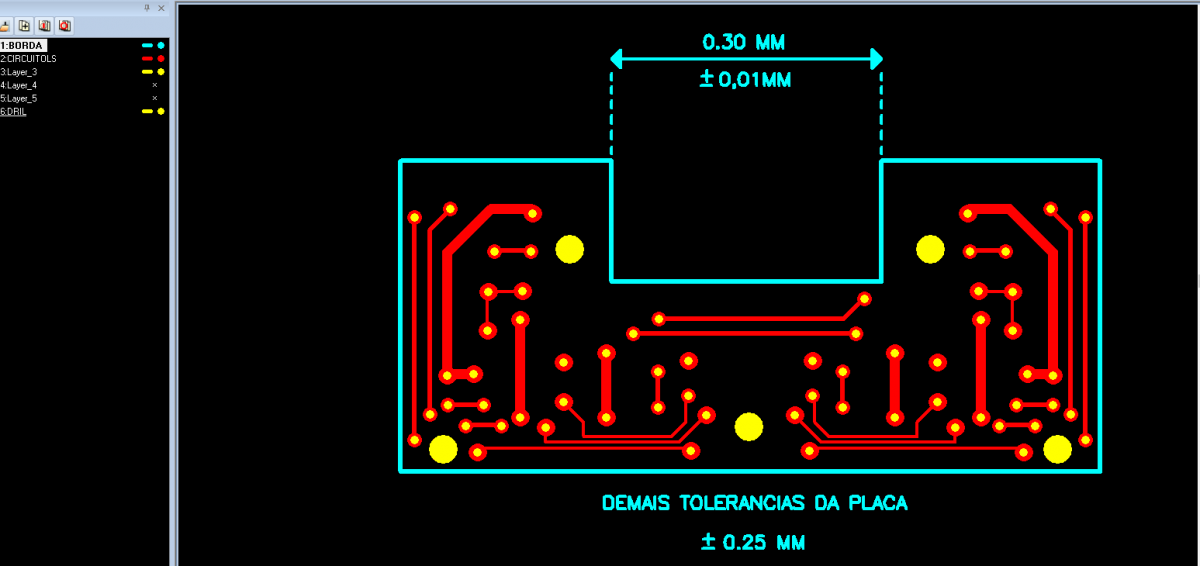
Tolerâncias intoleráveis
8 – Dimensões VS Número de faces
É óbvio que quanto menor o tamanho da placa, menor será o seu custo. Também é certo que quanto menor o número de layers, o mesmo ocorrerá. Então sempre que possível reduzir ambos, a economia estará garantida. Mas existem situações onde um pequeno aumento na área da placa pode permitir que uma placa inicialmente prevista em duas faces seja executada sem perda de qualidade em apenas uma face. O oposto também pode ocorrer, uma placa face simples pode ter sua área significativamente reduzida se transformada em dupla face.
Na primeira situação, a chance de redução de custo é bem maior, então um crescimento de área, mesmo que significativo, poderá ser economicamente viável. Já no segundo exemplo, será necessária uma redução de área grande para se obter um custo menor, pois as placas dupla face tem naturalmente um preço por área mais elevado.
Por isso, antes de se pensar em uma alteração no projeto, é necessário mais uma vez a simulação de cotações que identifiquem a melhor opção. Você pode realizar essa cotação sem compromisso aqui na TEC-CI, com nosso auxílio de como produzir as suas placas com o menor custo e com a mesma qualidade de sempre!
E além dessas dicas de como conseguir importantes reduções de custos desde a geração do layout da sua placa, conte com a equipe da TEC-CI Circuitos Impressos, sempre pronta para te orientar no que for possível, atingindo sempre a maior produtividade e competitividade nos seus produtos. Foi assim que crescemos junto com nossos clientes, colocando à sua disposição a nossa experiência e dedicação.