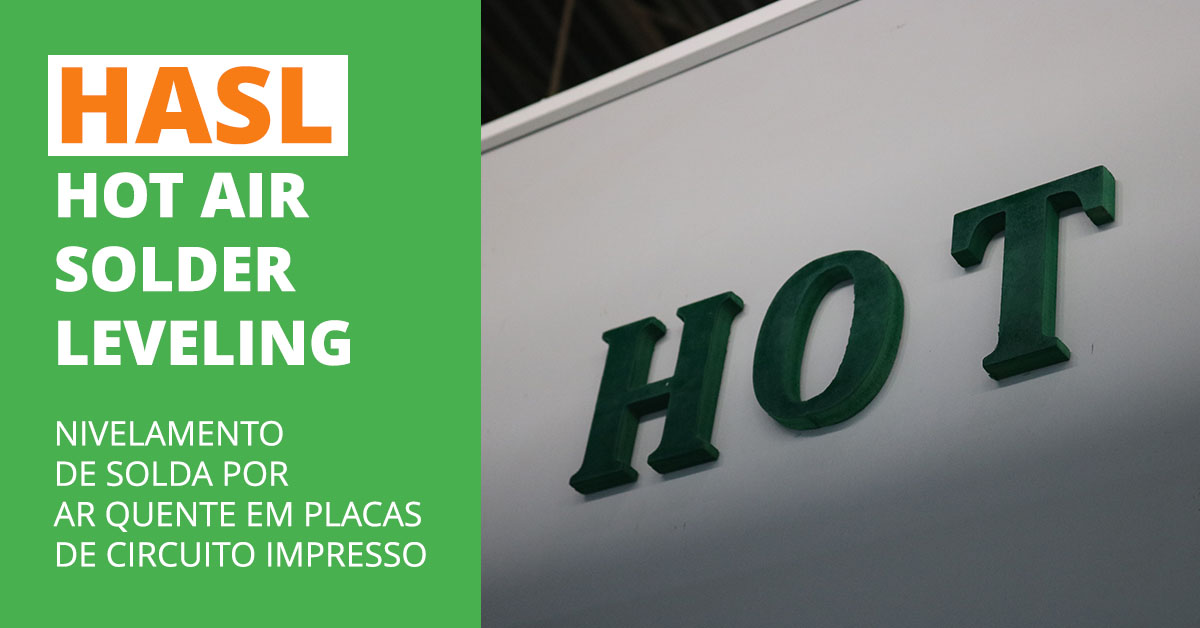
Um dos principais problemas que motivaram a criação do processo de nivelamento de solda por ar quente, foi a grande dificuldade de manter a aderência das máscaras anti-solda sobre as trilhas das placas durante o processo de soldagem em máquinas de solda à onda. Isto porque além dos furos metalizados receberem uma camada de estanho, as trilhas também recebiam essa camada no mesmo processo.
A máscara anti-solda era aplicada então sobre as trilhas estanhadas e, apesar dos esforços para se conseguir uma tinta que não se movimentasse durante o processo de soldagem das placas, nada era realmente eficaz.
Ao se submeter a placa à soldagem por onda, o estanho que cobria as trilhas, sujeito à mesma alta temperatura, acabava se movimentando e destruindo a máscara anti-solda.
Além desse problema, o surgimento da tecnologia de montagem SMT, exigia que a superfície a ser soldada apresentasse ao menos uma planicidade que não atrapalhasse o processo.
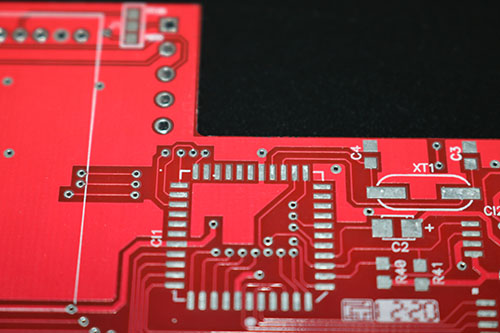
Com essas duas dificuldades a serem resolvidas, somente uma ótima solução poderia surgir para revolucionar a forma de se fabricar as placas de circuito impresso nesse processo. E essa ideia era o HASL, popularmente chamado de “hot air”, ou simplesmente “hot”.
O estanho depositado por eletrólise nas placas hoje em dia só tem a função de proteger o cobre durante o processo de corrosão. Por isso, logo após esse processo é retirado para que a máscara anti-solda seja impressa somente sobre o cobre, que por ter um ponto de fusão muito mais elevado que o estanho, não se movimenta durante a soldagem, mantendo a máscara anti-solda em perfeito estado.
Mas a proteção do cobre exposto nas ilhas e pads e também nas paredes dos furos se faz necessária. E ela, além de não poder bloquear os furos, também não pode prejudicar a planicidade dos pads, sobretudo nos casos em que se tem pads extremamente pequenos.
Com isso, o processo de “hot air” conseguiu atender à grande maioria dos casos, deixando um pouco a desejar somente em casos de pads extremamente pequenos, como por exemplo nos terminais de BGAs, que necessitam de soluções como o OSP ou enig.
Mas além disso, no caso das placas de uma única face, quando comparamos com o verniz pró soldagem, o “hot air” apresenta grande vantagem, tanto em velocidade do processo de soldagem, quanto na maior confiabilidade. Isso traz uma grande diminuição dos pontos de falhas de soldagem, reduzindo muito os processos de inspeção e retoques. É claro que o custo é um pouco mais elevado, porém, quando a placa possui pontos de solda mais reduzidos, isso é um diferencial bastante importante.
O processo de aplicação do "HOT AIR" passa por algumas etapas:
Após a aplicação da máscara anti-solda, que deve ser curada de forma perfeita para se evitar destacamento durante a aplicação do “hot air”, as placas são submetidas a um processo de desoxidação do cobre. Isto ocorre devido ao aquecimento presente no processo de cura da máscara anti-solda.

Após essa desoxidação, é aplicada uma fina camada de um fluxo similar aos utilizados na montagem da placa. As placas são mergulhadas verticalmente por um braço mecânico num reservatório cheio de estanho a elevadas temperaturas. Após poucos segundos submersas, as placas sobem recebendo um forte jato de ar também aquecido e perfeitamente direcionado por duas facas de ar, uma a cada lado da placa. Elas são cuidadosamente posicionadas em ângulos ajustados, para nivelarem e fazerem uma varredura do estanho ainda em estado líquido. Isto é feito sobre a superfície dos pads e também retirando completamente qualquer resíduo de estanho do interior dos furos.
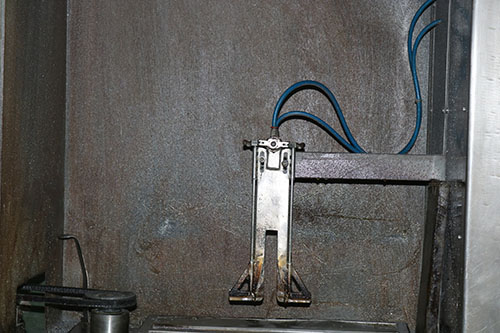
Após isso, a placa é resfriada e submetida a um desengraxante que remove todo o excesso de fluxo ainda remanescente, apresentando assim um aspecto brilhante e que gera uma excelente soldabilidade durante sua montagem.
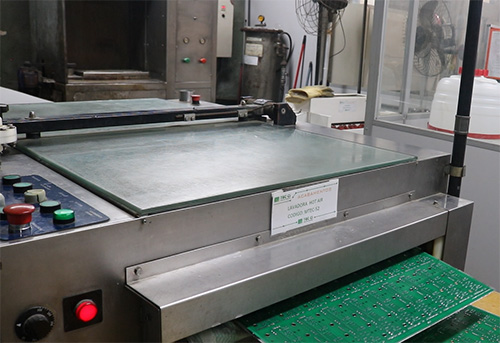
Com o objetivo de se atender às normativas RoHS no que se refere à extinção da presença de chumbo nas ligas de estanho (lead free), foi necessário que os equipamentos que aplicam esse processo fossem reestruturados. Isto porque a temperatura necessária para se trabalhar com as ligas de estanho sem chumbo são significativamente superiores, o que levou a novos projetos de equipamentos com reservatórios de paredes mais grossas, resistentes a essas altas temperaturas, bem como resistências e bombas especiais para suportar todo o processo.
Se você ainda não conhece este processo, não deixe de ver o nosso vídeo mostrando detalhadamente todo esse passo a passo. Qualquer dúvida que permanecer, conte sempre com a TEC-CI para esclarecer!