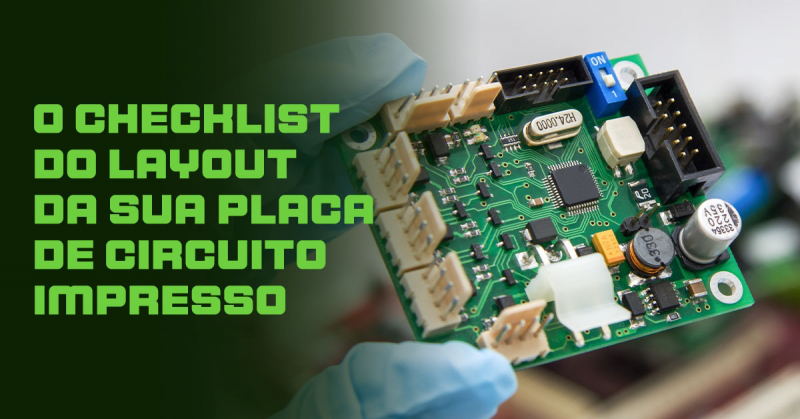
É muito comum recebermos layout com algumas correções que se fazem necessárias para uma produção de placas com maior produtividade e melhor qualidade. Por essa razão, sempre checamos todos os layouts recebidos antes de iniciarmos a produção.
No entanto, há diversos detalhes importantes que não nos permitem detectar a existência de alguma anormalidade, que muitas vezes pode até inviabilizar o funcionamento e a utilização das placas. Por isso, sempre recomendamos uma cuidadosa verificação de todo o layout para evitar problemas.
É claro que de acordo com as especificações de cada placa, essas verificações variam. Mas para auxiliar, vamos passar a seguir um checklist dos principais pontos em que essa verificação deve ser focada.
E se precisar de mais detalhes sobre os processos produtivos relacionados a cada etapa de verificação, basta clicar nos links que levarão aos nossos artigos e vídeos disponíveis.
Verificações de posicionamento de componentes
Os arquivos 3D são muito reveladores neste processo. E os softwares EDA mais modernos contam com versões muito nítidas que dão uma visão bastante precisa do posicionamento dos componentes. Através deles, você consegue verificar detalhes importantes que vão auxiliar na avaliação em diversos aspectos. Nesta observação deve-se prever a necessidade de substituição de componentes devido à indisponibilidade de determinados fornecedores. Nestas substituições, conforme o componente, é possível encontrar encapsulamentos de dimensões diferentes e prever a possibilidade de utilizá-los deixando um espaço que permita isso, apenas para esses componentes suscetíveis a essas indisponibilidades.
O fácil acesso a eventuais manutenções e medições que possam ser necessárias, também precisa ser pensado e conforme o posicionamento dos componentes, esse acesso pode ser prejudicado.
Um cuidado especial com os posicionamentos dos conectores é muito importante. Além de questões de acesso, muitas vezes impedidos por componentes de altura superior, diferenças de medidas entre o contato que vai na placa e seu par podem comprometer o layout, e até mesmo a inversão acidental de lado não é tão rara assim de acontecer. Então se sua placa tem conectores, a atenção especial a eles nunca será demais.
Outras verificações também ficam mais simples, como o posicionamento dos capacitores de desacoplamento próximos aos pinos de alimentação. O afastamento suficiente entre o circuito analógico e o digital, entre outros aspectos, também garantirão o sucesso do seu layout.
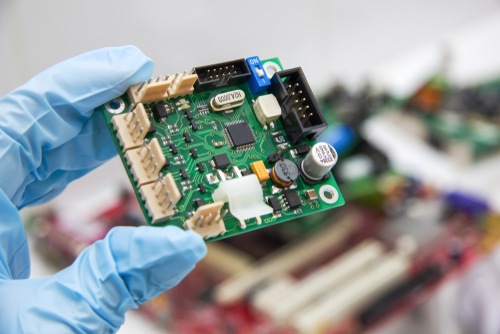
Verificações de Roteamento
A largura das trilhas e os espaçamentos na placa são dos pontos mais importantes a serem observados. Regras de design (DRC – verificação de regras de design) precisam ser ajustadas de forma que se tenha condições de praticar um roteamento adequado às necessidades de interconexões do circuito, sem comprometer ou dificultar a fabricação da placa de circuito impresso. A definição numérica de larguras e espaçamentos mínimos aceitáveis pelos fabricantes de placas é algo bastante relativo, pois esses limites podem não ser viáveis se presentes em grandes áreas da placa. O oposto também é válido: alguns limites numéricos podem ser aceitos desde que sejam em um ou alguns poucos pontos específicos dentro da placa. Portanto, revisar toda a rede de trilhas é muitas vezes mais determinante do que basear-se somente nas respostas obtidas pelo DRC que, é claro, ajuda demais nessa avaliação.
Uma atenção especial deve ser tomada nos casos de placas com espessura de cobre diferente, como por exemplo, os cobres de 2 onças (70 mícrons), que necessitam de um espaçamento maior.
Nesta etapa da verificação, deve-se observar a possível presença de ligações com trajetos maiores que os necessários, sobretudo em circuitos com sinais de alta velocidade. A presença excessiva de vias muitas vezes desnecessárias também pode afetar este aspecto.
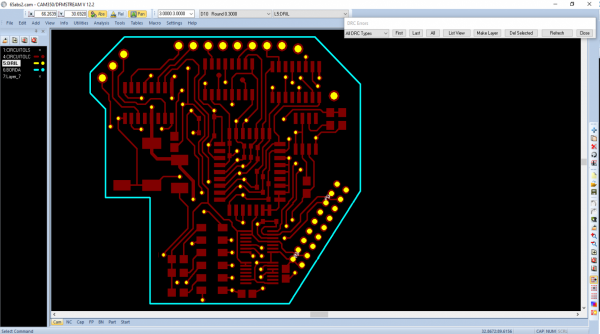
Verificações de máscara anti-solda e pasta de solda
A própria composição da tinta da máscara anti-solda utilizada em processos de aplicação por serigrafia, faz com que a máscara invada, ainda que minimamente, a área das ilhas e PADS a serem soldados. Por isso é que se faz necessário que o design da máscara observe uma certa expansão que permita alguma folga em relação às ilhas e PADS. Mesmo nos processos fotográficos em que não existe essa migração da tinta sobre o cobre, há esta necessidade, uma vez que tanto na exposição aos raios ultravioleta quanto na revelação, alguma perda sempre acontece e a invasão da área de solda também ocorre. Portanto verificar se esta folga foi observada é muito importante.
A verificação geral de todos os componentes, com atenção especial aos SMD, que além da abertura da máscara, devem ter definida a aplicação da pasta de solda em seu respectivo layer.
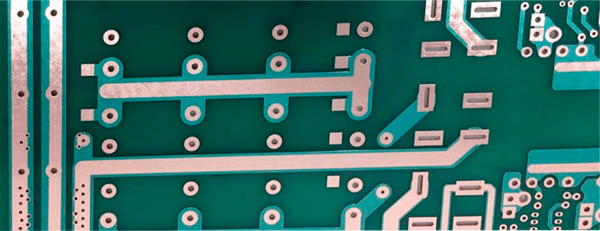
Verificação da Legenda de componentes
Embora menos importante para o funcionamento da placa, a quantidade de informações trazidas pela legenda de componentes faz com que a atenção nesta verificação não possa ser desprezada.
O posicionamento dos caracteres, todos voltados para os mesmos lados e de acordo com a melhor posição para a montagem, manutenção ou a própria visualização em campo, no caso de placas que ficam expostas, precisa ser considerada.
O tamanho ideal desses caracteres também deve ser levado em conta, pois podem determinar a legibilidade e, às vezes, a própria aparência da placa.
O posicionamento de todo o design precisa ser bem verificado. É muito comum encontrarmos traços ou caracteres sobrepostos a áreas cobreadas, prejudicando a soldabilidade e comprometendo o processo de montagem.
É na legenda de componentes que se tem a possibilidade de apresentar informações importantes como datas, números de revisão, número de série, e em alguns casos, até temas comerciais como logotipo, site e dados de contato.
E mais importante ainda que tudo isso, é verificar a correta indicação não só do posicionamento do componente como também de sua pinagem e polarização. Além disso, qualquer indicação que facilite a montagem ou mesmo a futura manutenção que possa ser necessária como, por exemplo, o tamanho e amperagem de um fusível.
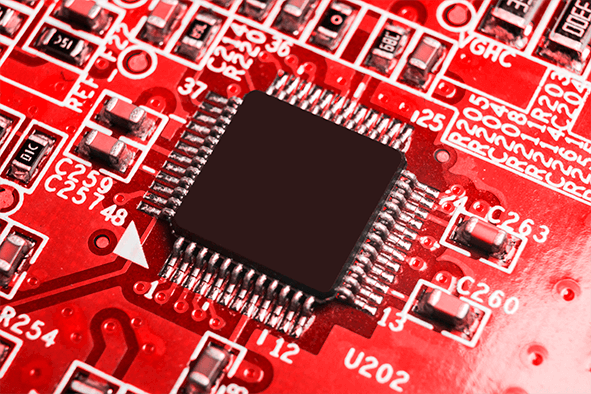
Verificação da furação
Há diversas verificações necessárias somente na furação. Furos sobrepostos podem gerar custos e quebras de brocas, além da ampliação de prazos de entrega. Ou seja, eliminá-los é muito importante.
A presença muitas vezes desnecessária de inúmeros diâmetros diferentes de furo que poderiam ser agrupados reduzindo essa variedade de medidas também traz essas mesmas vantagens.
Uma legenda de furação com símbolos que determinam cada diâmetro, bem como a quantidade de furos de cada um desses diâmetros, ajudará a eliminar qualquer dúvida nem sempre clara no arquivo de furação. Especificar claramente a presença de furos metalizados ou não metalizados é também essencial.
A determinação de tolerâncias claras e somente as realmente necessárias é fundamental. Pois uma tolerância que esteja determinada por padrão apenas, e que seja muito pequena, poderá requerer adaptações ao processo normal de furação que gere novamente custos e maiores prazos de entrega.
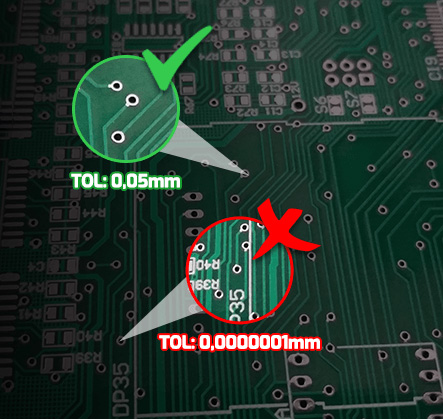
Verificações mecânicas
As dimensões da placa precisam não apenas ser verificadas como também mencionadas claramente e preferencialmente em milímetros. Tolerâncias devem ser apontadas, mas apenas em caso de necessidades críticas em que variações de alguns poucos décimos de milímetro possam dificultar ou impedir a acondicionamento da placa em seu gabinete ou local de uso.
Em caso de placas a serem montadas em painéis vincados, é muito importante a verificação dos principais elementos que determinarão essa montagem e sua posterior depanelização. As abas e suas dimensões e sentidos precisam ser verificadas, além de eventuais furos presentes nessas abas ou ainda fiduciais que auxiliem na leitura ótica dos equipamentos de montagem.
A determinação da espessura do laminado, sempre que fora do padrão que é de 1,6mm, precisa estar clara desde o orçamento da placa — mas sua especificação no plano mecânico também é importante.
E em casos que fujam ao padrão normal de espessura da placa, bem como em casos de situações específicas, a profundidade do vinco precisa ser determinada.
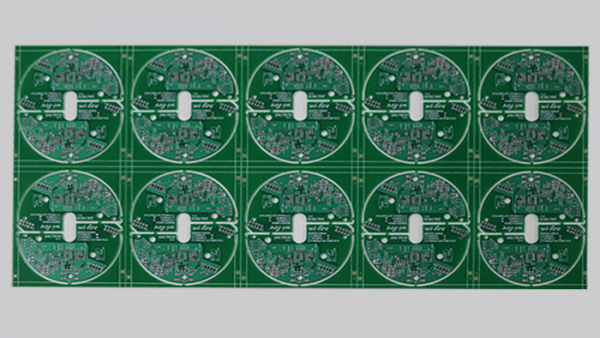
Verificação de arquivos de produção
Ao gerar os Arquivos Gerber é importante verificar a seleção de todos os arquivos de produção a serem enviados para a fabricação. Além dos layers do circuito, máscara e legendas de componentes, não se pode esquecer dos arquivos de furação e contorno das placas, bem como sempre será bem-vindo um arquivo extra do tipo leia-me. Este contendo informações adicionais como cor da máscara anti-solda, da legenda de componentes, espessura da placa, espessura do cobre, ou qualquer outra informação que possa ser útil, inclusive um contato do profissional que esteja habilitado para tirar dúvidas de forma mais rápida e direta. Dessa forma haverá muito mais agilidade na solução dessas eventuais dúvidas, acelerando o processo de produção das suas placas de circuito impresso.
Lembrando que relacionamos aqui apenas as verificações mais básicas e inerentes exclusivas à fabricação das placas de circuito impresso. Elaboramos abaixo um quadro para você usar como um checklist do seu layout, que pode ser muito útil para juntos alcançarmos a maior agilidade e qualidade possível nas suas placas.
Checklist do layout e informações para a fabricação de circuitos impressos
1. Posicionamento de componentes
- Possibilidade de substituição de componente
- Acesso a manutenções e medições
- Facilidade de montagem
- Atenção especial a conectores
- Posicionamento de componentes específicos
- Separação de circuitos analógicos e digitais
2. Roteamento
- Avaliar possibilidades de redução de trajetos
- Abertura da máscara anti-solda
- Verificação de aberturas ausentes
- Analisar o resultado do DRC
3. Máscara anti-solda
- Largura das trilhas e espaçamentos
- Aplicar o DRC
- Verificação específica dos PADS de SMD
4. Legenda de componentes
- Posicionamento e sentido dos caracteres
- Tamanho e legibilidade dos caracteres
- Sobreposições de traços ao cobre
- Informações adicionais
- Indicações de polaridades, posicionamentos e valores
5. Furação
- Furos sobrepostos
- Diâmetros agrupáveis
- Legenda de furação
- Furos não-metalizados
- Tolerâncias
6. Verificações mecânicas
- Dimensões da placa
- Presença de abas
- Furos ou fiduciais para montagem
- Espessura do laminado
- Formato avulso/painel vincado
7. Arquivos de produção
- Arquivos Gerber
- Arquivo de furação
- Arquivo de contorno
- Arquivo extra de informações e contato