
Parte 1 – Face simples
Existem inúmeras formas de se fabricar placas de circuito impresso de forma artesanal e muitas delas ajudam a resolver necessidades específicas, quando falamos de algumas poucas unidades de placas. Mas quando se trata de lotes maiores, essas formas artesanais se tornam inviáveis. Portanto, somente uma produção em escala industrial apresentará essa viabilidade.
A seguir vamos descrever de forma sucinta a sequência dos processos de fabricação industrial. Desde já, esclarecemos que esta sequência é a mais comumente verificada na maioria dos casos, podendo apresentar variações de acordo com as características de cada placa, bem como de cada fabricante de placas de circuito impresso.
Como sabemos, tudo começa na geração do layout do circuito. Este layout gera arquivos de imagem e arquivos de controle numérico que orientarão todo o processo.
Os arquivos de imagem de um modo geral são compostos pelas imagens das trilhas do circuito, bem como da máscara anti-solda e da legenda dos componentes. Esses arquivos são enviados a uma fotoplotter a laser, que gera os fotolitos utilizados na confecção de telas serigráficas, usadas na transferência da imagem para as placas. Mas para circuitos mais críticos, com trilhas e espaçamentos mais finos, essa transferência é fotográfica, o que explicaremos melhor na segunda parte deste artigo sobre fabricação de placas de circuito impresso.
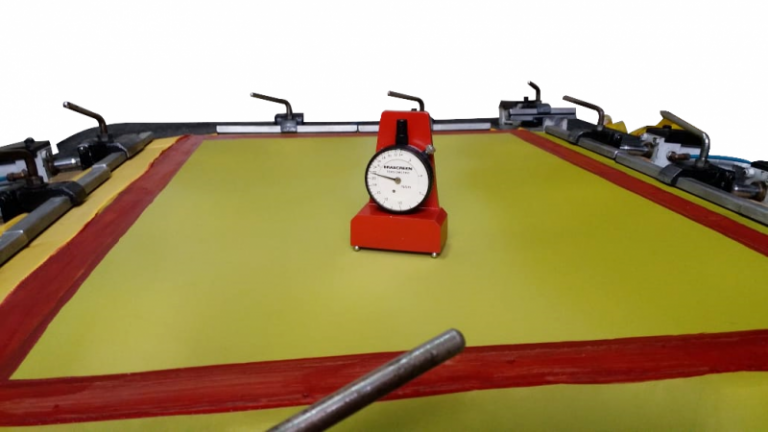
Paralelamente à confecção dessas telas serigráficas, é efetuado o corte inicial da chapa do laminado, que para circuitos de uma face, geralmente é um laminado de fenolite, composite, fibra de vidro ou metalcore. Ele é prensado com uma folha de cobre em sua superfície de aproximadamente 35 mícrons de espessura.
Este corte inicial divide a chapa em painéis de produção, onde programa-se a disposição de várias imagens do mesmo circuito com o intuito de se aumentar a produtividade.
Uma vez cortados, esses painéis de produção seguem para a furação, no setor de CNC. Inicialmente são executados furos em suas extremidades, onde são inseridos pinos guia, que servirão para agrupar “sanduíches” de 3 ou 4 placas, e também para aumentar a produtividade. Esses pinos se sobressaem deste “sanduíche” para serem fixados nas guias das mesas das furadeiras comandadas por controle numérico (CNC), que executam toda a furação da placa. Os arquivos de comando numérico de coordenadas mecânicas gerados lá no layout, são carregados neste equipamento. Essas coordenadas são agrupadas separadamente para cada diâmetro de furo diferente na placa, e o equipamento identifica através do software, executando a substituição da broca para cada diâmetro. É um processo totalmente automatizado e com uma velocidade surpreendente.
Após concluída a furação, os pinos guia são retirados e os painéis seguem para um polimento de sua superfície que conta com jatos de alta pressão e escovas de nylon, que ajudam a eliminar qualquer resíduo da superfície cobreada da placa e também do interior dos furos.
Com a superfície do cobre em perfeito estado e sem qualquer impureza, as placas seguem para receber a imagem do circuito com suas trilhas, pads e ilhas que coincidirão perfeitamente com o posicionamento dos furos existentes na placa.
Isso acontece através da perfeita centralização da matriz serigráfica que deve contar com excelente precisão. Por isso, são confeccionadas com quadros de alumínio e tecidos de extrema estabilidade dimensional. Uma vez centralizada a tela com relação à placa sobre uma mesa serigráfica, a repetibilidade do posicionamento da imagem sobre todas as placas é garantida por registros de posicionamento por leitura óptica, ou mesmo por pinos guia fixados à mesa. Eles coincidem com furos inseridos no painel de produção especificamente para esta função.
A tinta aplicada por serigrafia sobre o cobre é uma tinta resistente ao ataque do corrosivo (Etch-resist). Sua cura pode ser em temperatura ambiente, por aquecimento térmico, ou através de raios ultravioleta, o que garante maior velocidade ao processo e confiabilidade na aderência da tinta à superfície do cobre. Isso permite, inclusive, o empilhamento das placas logo após a cura, o que facilita todo o fluxo de produção.
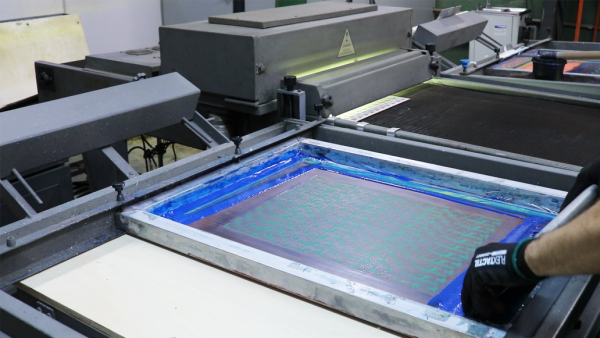
Após uma boa inspeção óptica dessa impressão, as placas seguem para a corrosão, onde o corrosivo irá retirar todo o cobre da placa, exceto aquele que está sendo protegido pela tinta. Isto acontece em uma corrosora, composta por uma esteira horizontal, por onde prosseguem as placas até adentrarem numa câmara, onde jatos desse corrosivo são lançados sobre as placas sob alta pressão, efetuando assim a rápida remoção do cobre exposto na placa.
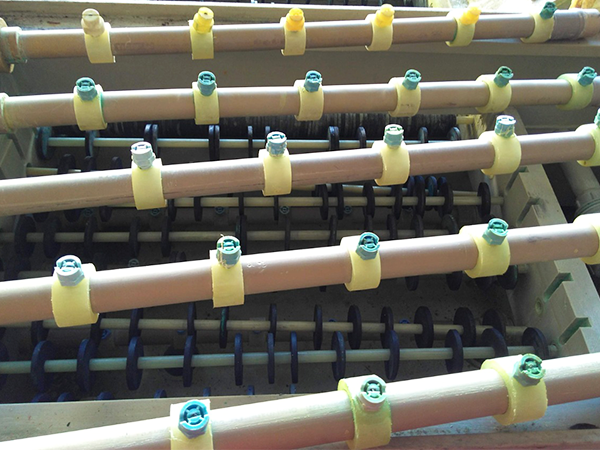
Esse corrosivo pode ser o conhecido percloreto de ferro. Porém, hoje em dia, quase não é mais utilizado em escala industrial, tanto pela menor velocidade que ele oferece ao processo, quanto pelo seu alto custo ambiental. Isso porque ao estar exaurido, antes de seu descarte, precisa passar por um processo bastante complicado para a retirada do cobre, o que é muito mais simples com corrosivos alcalinos à base de amônia, que hoje predominam nas fábricas de circuito impresso.
Concluída a corrosão, uma nova e rápida inspeção é feita e não havendo nenhuma imperfeição no processo, a placa prossegue ainda pela mesma esteira, penetrando em uma nova câmara, para que a tinta que protegia o circuito seja removida também através de jatos de alta pressão de hidróxido de sódio. Ela prossegue então sempre pela mesma esteira pelo módulo de neutralização desses produtos químicos, lavagem e secagem, saindo de toda essa sequência já com o circuito em cobre totalmente definido, idêntico ao que foi projetado.
Após todos esses processos, o cobre já estará naturalmente oxidado pela ação dos produtos, e com isso se faz necessário um novo polimento antes da aplicação da máscara anti-solda.
Desta forma, é utilizada uma escova um pouco menos abrasiva e com uma intensidade também reduzida para preservar ao máximo a integridade das trilhas em cobre.
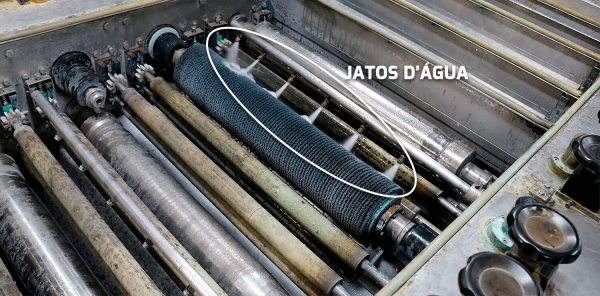
A aplicação da máscara anti-solda ocorre num processo similar à aplicação da imagem do circuito, também por serigrafia, com os mesmos cuidados de centralização adotados na primeira impressão. Apenas a tinta é que possui características específicas para suportar as altas temperaturas a que será submetida durante a soldagem das placas. Também são curadas mais comumente por raios ultravioleta em esteira com velocidade ajustada para uma perfeita cura. A tradicional cor verde da máscara anti-solda continua predominando, mas são cada vez mais comuns placas com máscara em diversas outras cores.
A aplicação da legenda dos componentes, no caso de circuitos PTH, pode ocorrer antes ou após a aplicação da máscara anti-solda, também pelo processo serigráfico. Mas para circuitos smd ou mistos, essa impressão ocorre sobre a máscara anti-solda, e também por serigrafia.
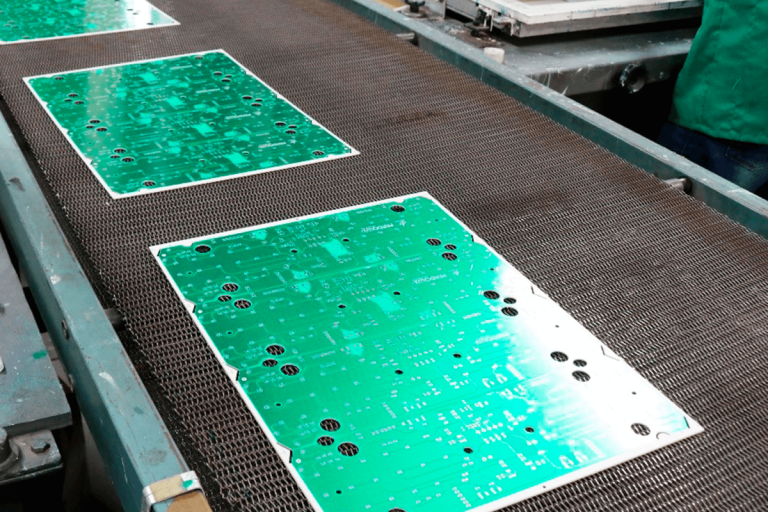
Depois disso, as ilhas e pads que ficaram expostos após a aplicação da máscara e da legenda, estarão certamente com alguma oxidação, mesmo que imperceptível a olho nu. Então passam novamente por uma esteira e entram numa câmara que irá jatear um desoxidante, para que, ao se aplicar o acabamento de superfície final, o cobre esteja em perfeito estado para permitir uma excelente soldabilidade em seu processo de montagem.
O acabamento de superfície tem algumas opções, sendo que a mais comum para circuitos de uma face é o verniz pró soldagem, que é aplicado em envernizadeiras, através de rolos emborrachados. Outra opção bastante utilizada é o HASL, (Hot air Solder Leveling). Neste caso, além do desoxidante, as placas passam ainda por um processo de fluxagem antes de serem mergulhadas no tanque aquecido de estanho no equipamento de hot air.
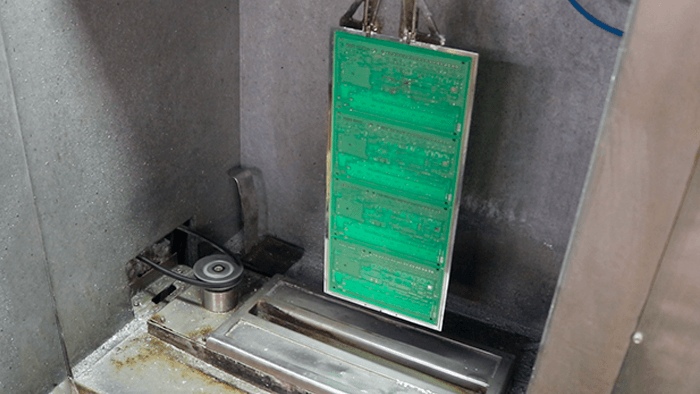
Após o acabamento de superfície temos o corte final, pois os painéis precisam ainda ser divididos de acordo com as dimensões de cada placa contida neste painel. Essa divisão pode ser feita em corte simples em guilhotina. Porém, há casos em que os cortes retos em guilhotina não atendem a necessidade como cortes internos, cortes em “L”, “U” e outras situações em que as placas precisam ser fresadas nos equipamentos de CNC.
E há também uma opção muito utilizada, em que os painéis de produção são entregues inteiros, com todas as placas presentes, sendo apenas vincadas por um disco de corte, que secciona parcialmente as placas em sua espessura. Assim, mantendo uma alma interna de material que possibilite a posterior separação das placas. Com isso, a montagem dos componentes e a soldagem podem ser executadas em painéis, ganhando muito em produtividade e, uma vez concluída a montagem, executa-se a separação das placas unitárias.
Após efetuada uma das opções de contorno, as placas passam então pelo controle de qualidade final, que é determinado conforme a complexidade do circuito. Circuitos mais simples podem ter controle de qualidade visual humanizado com equipamentos específicos de iluminação e lupas especiais para essa finalidade. Em caso de circuitos de complexidade intermediária, adota-se processos de inspeção óptica automatizada. Já para circuitos de alta complexidade, utiliza-se equipamentos de teste elétrico que são capazes de garantir 100% o funcionamento das placas.
Como dissemos, de acordo com características e detalhes específicos de cada placa e de cada fabricante de placas de circuito impresso, esses processos podem sofrer alguma alteração. Porém, na grande maioria dos casos que fabricamos em nosso dia a dia, esta é a sequência de processos adotada.
Se tiver qualquer dúvida sobre a fabricação de placas de circuito impresso, entre em contato com a TEC-CI CIRCUITOS IMPRESSOS. Estaremos sempre à sua disposição!
E se preferir, assista aos vídeos da nossa série completa sobre a fabricação de placas de circuito impresso.
Em breve, não deixe de conferir aqui mesmo em nosso Blog a segunda parte do artigo, onde descreveremos todos os processos de fabricação das placas de duas faces com furos metalizados.